Objective
During manufacturing, processing and application, fluids are often exposed to complex flow fields. Particularly, those which contain extensional components, when the flow strongly converge as e.g. during filtration, in certain pump types or during industrial high speed coating processes. One calls the formation of aggregates in multi phase fluids, which are exposed to such a converging or elongational flow fields, flow-induced coagulation or aggregation. The ring-slit test has been developed in order to characterize the stability of colloidal suspensions and dispersions in converging flow fields, whereas the aggregates are simultaneously formed and “detected”.
Operating Principle
The ring-slit device is mounted to a piston driven capillary viscometer. A piston drives the sample to flow through the ring-shaped slit at the bottom end of the wall of a cylindrical sample chamber at a constant volumetric flow rate. A pressure transducer records the corresponding pressure as a function of extruded sample volume or time. If the sample is stable the pressure adjusts itself to a comparably low constant value determined by the viscosity of the particular sample. In this case the instrument operates as a high shear capillary viscometer and shear rates of more than 2 106 s-1 can be reached. If the sample is not stable a strong increase of the extrusion pressure with time is observed due to a gradually clogging of the slit cross-section by the agglomerates created in the converging flow field (90° deflection and converging streamlines) at the entrance of the slit. The volumetric flow rate can be varied in a broad range and so that it can meet the typical requirements of technical processes.
Fig. 1: Schematic drawing of a Ring-slit device, Elongational flow field in front of the slit entrance and pressure development for stable and unstable samples.
Specifications
Sample volume: |
150 mL |
Gap height: |
25 µm, 50 µm and others on request |
Applications
- Filtering and pumping of dispersions and suspensions
- Ring-slit test of paints and varnishes
- Flow-induced aggregation of coating colours and adhesive-dispersions by high speed coating processes
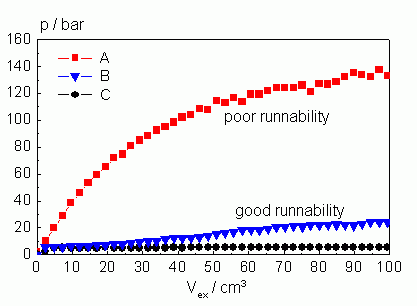
Fig. 2: Flow-induced aggregation and runnability of paper coating colours. Poor runnability means accumulation of aggregates at the exit of the blade and correspondingly strongly pressure increase. Good respectively poor runnability refer to machine coating trials with a stiff blade. The machine speed is set to 1600 m/min and the application weight is 7 g/m³.
Literature
- Runnability and Flow-induced Aggregation of Paper Coating Colors,
R. Ettl, V. Schädler, N. Willenbacher, Nordic Pulp and Paper Res. J., 5, 2000